We always recommend using a liquid nitrogen-cooled MCT detector for ATR-SEIRAS if available. If a MCT detector is not available, a room-temperature DTGS detector may be acceptable. A large number of co-added scans are required to achieve an acceptable signal-to-noise ratio, so the main consideration is the stability of the experimental system over the time required to collect the scans.
Here are two potential-difference absorption spectra comparing the performance of a DTGS detector to a MCT detector:
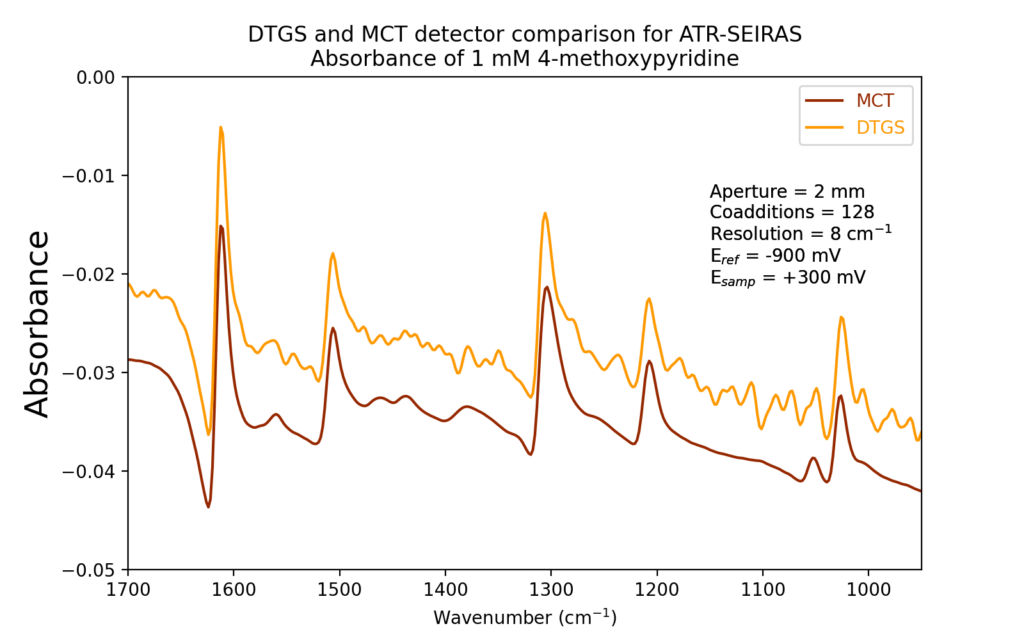
Experimental
An intrinsic, float-zone Si 35° microgrooved wafer was sputtered with 15 nm of indium tin oxide (ITO) and thermally annealed under vacuum at 300 °C for 1 hour. A gold nanoparticle film was electrodeposited onto the ITO film by applying a constant potential of -500 mV (vs sat. Ag/AgCl) and measuring the current until 5 mC of charge was delivered. The electrodeposition solution contained 0.2 mM KAuCl4 and 100 mM NaF.
The cell was emptied of the delectrodeposition solution, rinsed, and filled with 50 mM of NaF. 4-methoxypyridine was added to give a concentration of 0.1 mM. Potential-difference absorbance spectra were collected at -900 mV (reference spectrum) and +300 mV (sample spectrum).
A big thank you to Ariel Tirado for collecting these data.