The topic of preparing internal reflection elements (IREs) for thin film deposition comes up from time to time and we thought it might be helpful to address it in a blog post. The level of cleanliness required depends on the application and the method of deposition. Electrolessly deposited films require scrupulously clean surfaces, while the cleanliness conditions are relaxed somewhat if a conductive metal oxide underlayer is used for electrodepositing a metal film. This short article describes what works for us, but your mileage may vary.
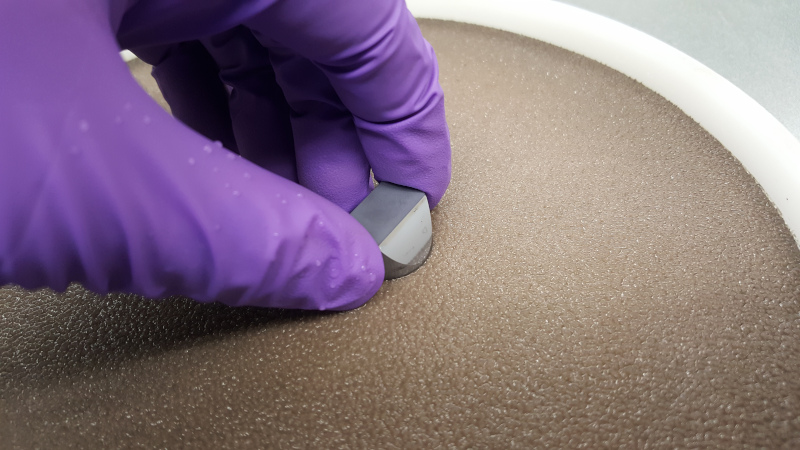
Assuming there are no major visible scratches in the IRE, you shouldn’t need to use any polish coarser than about 3 micron. We use polycrystalline diamond suspensions to polish the crystals, such as the DIAMAT line of products from PACE Technologies (no affiliation with Jackfish SEC). We polish in two steps: first with 3 micron, and then follow it with 0.5 micron. It’s possible to go even finer if your application calls for it. A cloth polishing pad is wetted and charged with the polish. Separate polishing pads should be used for each different grit. Applying light pressure and using a figure-8 motion, the crystal is lapped against the polishing pad. Too much water may cause the crystal to hydroplane across the surface of the pad without any polishing action.
It’s important to take care to avoid contaminating the finer grits with larger abrasive particles. When changing grits, it’s a good idea to take a new pair of gloves and wipe down the work surface. Long sleeves can be a culprit for transferring abrasive particles, so it’s best to roll them up or avoid baggy sleeves.
IREs can take several different forms: hemispheres, face-angled crystals (FACs) or even micromachined silicon wafers. The grooved wafers are rather fragile and difficult to hold on to while polishing. Instead, the wafers can be immersed in a solution of aqua regia (3 parts HCl to 1 part HNO₃) to strip off any metal or conductive metal oxide on the surface. After mixing the aqua regia, wait for it to cool down to room temperature. In our experience, immersion in room temperature aqua regia for 5 minutes with gentle swirling is sufficient to completely remove a 25 nm thick ITO layer . Aqua regia can be used on FACs as well, however it should not be used on crystals which have an anti-reflection coating, since this can be damaged by concentrated acids. Also, one should never use acid to clean a ZnS or ZnSe prism which will dissolve the crystal and release toxic gases.
After removing the coating from the IRE (either chemically or by polishing), we typically ultrasonicate in ethanol and then in water using a Teflon beaker so that the crystals don’t chip against the side of the beaker. After each step, we rinse with copious millipore water and blow dry with clean, dry air or inert gas from a cylinder.
Considerations for conductive metal oxide coatings
In a previous post, we discussed our preferred method of using conductive metal oxide underlayers (such as ITO) as a means to electrodeposit metal films from electrolytes containing metal ions. If you have an ITO-coated IRE with electrodeposited metal, it can often be reused several times. Extended contact with electrolyte causes ITO layers to fail, so it’s best to disassemble the cell and store the ITO-coated IRE dry between experiments. Rinse the top surface with millipore water to remove residual electrolyte and blow dry gently with inert gas. Make sure nothing brushes against the top of the film (the lower o-ring can be a culprit), since this can damage the metal film which is fairly delicate.
If the SEIRAS performance starts to decline, or if you want a new metal film, it may be possible to remove the metal while retaining the ITO . Our electrodeposited metal films can be removed by gentle polishing with 0.5 micron grit for a short time while keeping the ITO intact. This may not be ideal from a contamination standpoint, although if you’re in a bind, it can extend the use of an IRE without requiring access to vacuum-deposition equipment.